أنظمة انتقاء المستودعات
بينما يشكل الانتقاء 55٪ من تكاليف تشغيل المستودع (التقرير السنوي لشركة MHI 2023) ، إنه أيضا محور دقة الوفاء. يقوم هذا الدليل بفك تشفير تقنيات الانتقاء من خلال ثلاثة أبعاد: اختيار الإستراتيجية, تكامل المعداتو موازنة الكفاءة من حيث التكلفة.
تقنيات الانتقاء التي تم فك تشفيرها
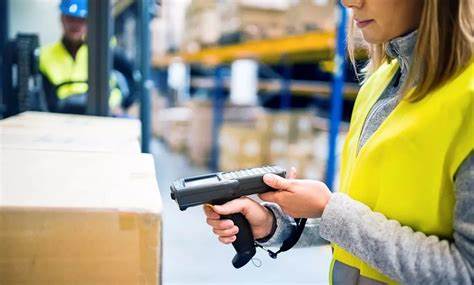
1. انتقاء الطلبات المنفصلة
â ̧ كيف يعمل
يقوم العمال باسترداد العناصر للطلبات الفردية بالتتابع. مثالي ل:
- السلع عالية القيمة (المستحضرات الصيدلانية / السلع الكمالية)
- أوامر مخصصة (قطع غيار ماكينات B2B) â ̧ تكديس التكنولوجيا
- سماعات رأس للانتقاء الصوتي (دقة 99.9٪)
- نظارات ذكية AR مع ملاحة HUD
2. انتقاء دفعات الكتلة
متري | الدفعة اليدوية | الدفعة الآلية |
---|---|---|
الطلبات / الساعة | 18 | 72 |
معدل الخطأ | 2.3% | 0.15% |
تكلفة العمالة | 8.5 دولار / طلب | 1.2 دولار / طلب |
نصيحة التنفيذادمج مع أجهزة الفرز عبر الأحزمة للحصول على عائد استثمار 4x في مراكز التجارة الإلكترونية.:
3. انتقاء التدفق الديناميكي
â1/4 خوارزمية تحسين تجمع الطلبات في الوقت الحقيقي
â1/4 متوافق مع أنظمة المكوك AS / RS (500 اختيار / ساعة)
â1/4 دراسة حالة: قلل موزع قطع غيار السيارات من وقت المشي بنسبة 83٪
مصفوفة المعدات
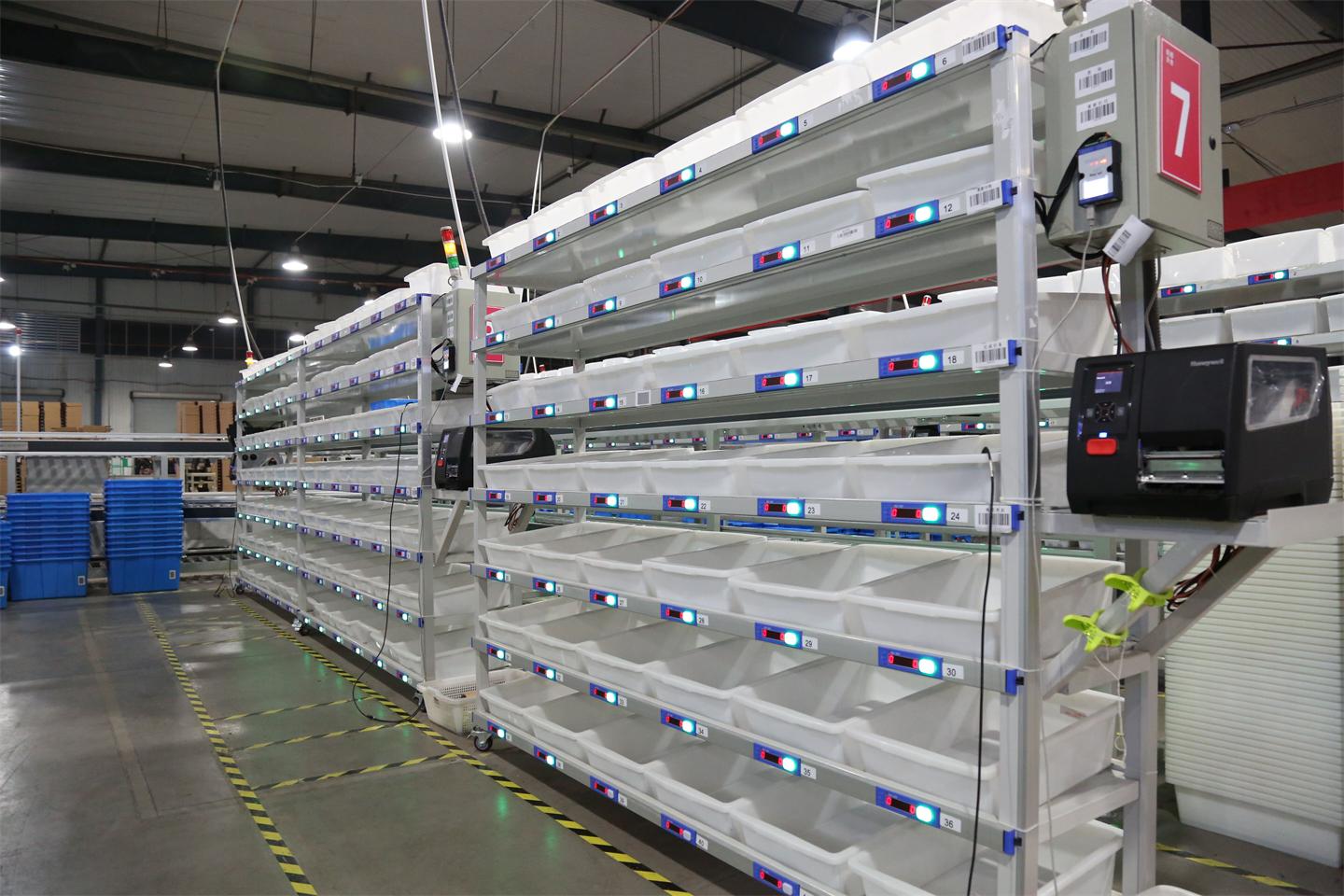
حلول من إنسان إلى بضائع
التقنية | الانتاجيه | أفضل ل |
---|---|---|
اختيار RFID للضوء | 220 سلع / ساعة | التخزين البارد للفارما |
ماسحات AR يمكن ارتداؤها | 180 سلع / ساعة | التعامل مع العناصر كبيرة الحجم |
عربات موجهة صوتيا | 300 سلع / ساعة | مستودعات متعددة المستويات |
أنظمة البضائع إلى الشخص
- مكوك AS / RSاستخدام المساحة بنسبة 98٪ (مقابل 40٪ تقليدي):
- AGVs على غرار Kiva: 1,500 اختيار / ساعة مع ذكاء السرب
- رفوف دوارة: 70٪ تقليل الطاقة مقابل أنظمة النقل
إطار التخطيط الاستراتيجي
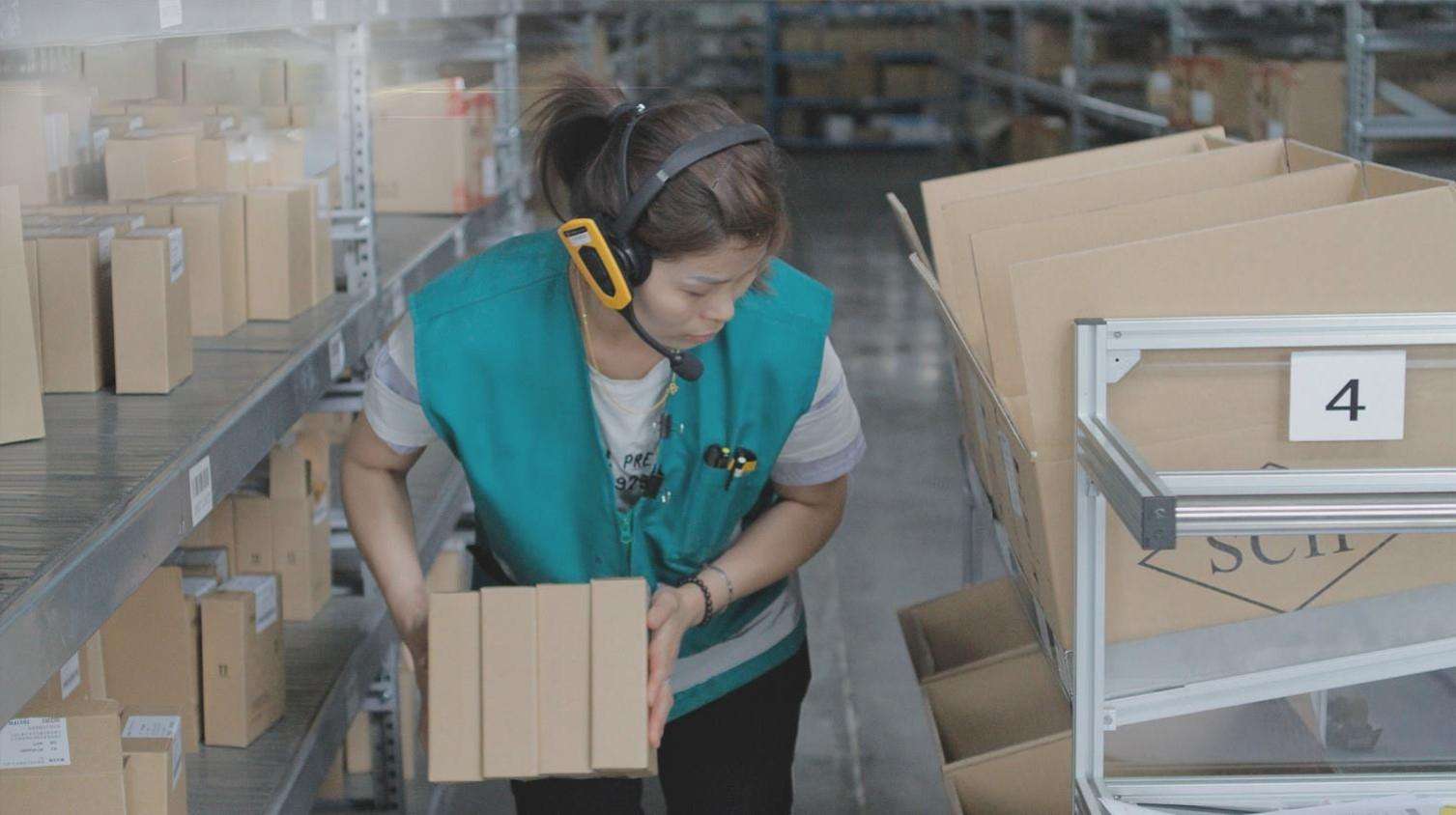
1. تحليل ملف تعريف الطلب
â1/4 رسم خرائط سرعة SKU (تحليل ABC)
â1/4 محاكاة ذروة الطلب (اختبار الحمل القائم على الذكاء الاصطناعي)
2. حاسبة التكلفة والعائد
مستوى الأتمتة | التكلفة المقدمة | إجمالي تكلفة الملكية لمدة 5 سنوات |
---|---|---|
الترددات اللاسلكية الأساسية | 15 ألف دولار | 82 ألف دولار |
AGV + WMS | 480 ألف دولار | 1.2 مليون دولار |
كامل AS / RS | 2.1 مليون دولار | 3.8 مليون دولار |
3. قيود التخطيط
- تباعد الأعمدة3.5 م كحد أدنى لأساطيل AGV:
- ارتفاع السقف: 9 م + لأنظمة المكوك المتعددة
- تحميل الطابق: 5 كيلو نيوتن / م² للمنصات الروبوتية